Note: Heating a copper end cap to melt wax
Objective:
To heat a copper end cap to temperature for a wax reflow application; the end product is a temperature stat and the client is looking to cut their heating time in half
End Product:
Copper end cap
Equipment:
Ambrell EASYHEAT 4.2kW, 150-400 kHz induction heating power supply with a remote workhead containing two 1.5 μF capacitors
A helical induction heating coil designed and developed specifically for this heating application
Materials:
End cap 0.5in (12.7mm) OD filled with wax
Temperature:
170 °F (77 °C)
Frequency:
400 kHz
Testing:
The end cap with wax was inserted into the coil and heated. The part was heated to temperature within three seconds. However, when the power was turned off, the part's temperature declined along the outside shell due to conduction through the part.
Consequently, the next step was to heat the shell and hold the temperature. A stepped heating profile was used to accomplish this objective. This proved successful, and the part can be held to temperature as long as necessary.
Benefits:
- Speed: The client's objective was for the part to heat to temperature within three seconds, and that was achieved thanks to the EASYHEAT being a more modern induction heating system and superior application design
- Precise, controllable heating: The client was able to achieve precise, controllable heating with induction, as the part can reach temperature and it can be held
- Minimal footprint: EASYHEAT induction heating systems require a minimal amount of space
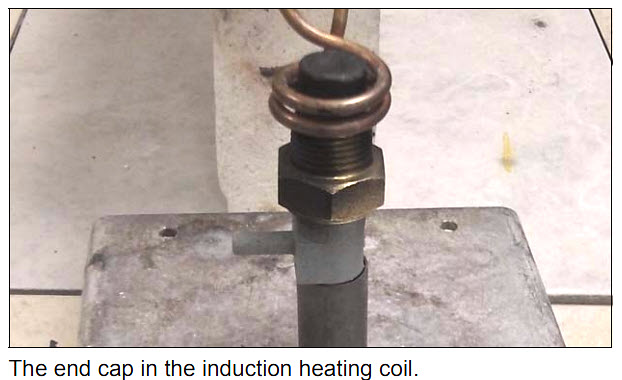
Visit our Applications Lab to learn more about free applications testing.
1655 Lyell Ave, Rochester, NY 14606 USA | Tel: +1 585 889 9000