What Is Induction Heating?
Induction heating is a precise, repeatable, non-contact method for heating electrically-conductive materials like brass, aluminum, copper or steel or semiconducting materials like silicon carbide.
Get our brochure to learn how induction can help...
How does induction heating work?
An induction heating system includes a special power supply which converts line power to a high frequency alternating current. This current is delivered over a specially-designed cable assembly to a workhead - or tank circuit - which creates an electromagnetic field within the attached coil. A work piece is placed in the coil, inducing an alternating current, causing friction and heat in the workpiece.
Induction heating is used very effectively in many processes like brazing, soldering and shrink fitting, from something as small as a hypodermic needle to a large wheel on a military tank. Many companies in the automotive industry, medical device industry and aeronautics make efficient use of induction heating in their processes.
More about how it works:
What's In an Induction Heating system?
Our induction heaters convert AC line power to a higher frequency alternating current, delivering it over a specially-designed cable to a workhead containing a bank of capacitors and a custom-designed work coil. This combination employs the principle of resonance to create an electromagnetic field within the coil to efficiently deliver energy to your workpiece.
The workpiece is placed in that electromagnetic field, inducing eddy currents in the workpiece. The friction from these currents generates precise, clean, non-contact heating. A water cooling system is generally required to cool the work coil and the induction heating system.

What Is Operating Frequency?
The operating or resonant frequency of an induction system is the point at which energy is most efficiently transferred.
The operating frequency is determined in the workhead by the capacitance of the tank circuit, the inductance of the induction coil and the material properties of the work piece.
Generally, for larger work pieces, lower frequency energy is required for deeper heating. For smaller work pieces, higher frequencies provide shallower heating.

Does Induction Heat Magnetic Materials?
If your work piece material is magnetic, such as carbon steel, it will be heated easily by induction’s two heating methods, eddy current and hysteretic heating. Hysteretic heating is very efficient up to the Curie temperature (for steel 600°C (1100°F)) when the magnetic permeability reduces to 1 and the eddy current is left to do the heating.

What Is the Heating Depth of Penetration?
This refers to how deeply induction heats the workpiece.
Induced current in the work piece will flow at the surface where 80% of the heat produced in the part is generated in the outer layer (skin effect). Higher operating frequencies have a shallow skin depth, while lower operating frequencies have a thicker skin depth and greater depth of penetration.
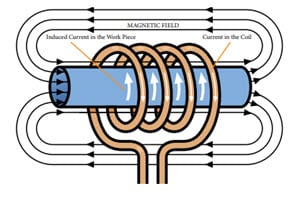
How Important Is Coupling Efficiency?
The relationship of the current flow in the work piece and the distance between the work piece and the induction coil is key; the closer the coil, the more current in the work piece.
But the distance between the coil and the work piece must first be optimized for the heating required and for practical work piece handling. Many factors in the induction heating system can be adjusted to match to the coil and optimize the coupling efficiency.

Is Coil Design Important in an Induction Heating System?
The efficiency of an induction heater is maximized if the work piece can be placed inside the induction coil. If your process won’t allow your work piece to be placed inside the coil, the coil can be placed inside the work piece.
The size and shape of the water-cooled copper induction heating coil will follow the shape of your work piece and be designed to apply the heat to the correct place on the work piece.

Power Requirements
The power required to heat your work piece depends on:
-
The mass of your work piece
-
The material properties of your work piece
-
The temperature increase you require
-
The heating time required to meet your process needs
-
The effectiveness of the field owing to the coil design
-
Any heat losses during the heating process
After we determine the power needed to heat your work piece we can select the correct induction heating equipment taking the coil coupling efficiency into consideration.
Is Induction Heating Cost-Effective & Energy Efficient?
Heat losses and uneven, inconsistent application of heat result in increased scrap and diminished product quality, driving up per-unit costs and consuming profits. Best manufacturing economies are seen when the application of energy is controlled.
To bring a batch oven up to temperature and to hold the entire chamber at the required temperature for the process time demands much more energy than is required to process the parts. Flame-driven processes are inherently inefficient, losing heat to the surroundings. Electrical resistance heating can also result in the wasteful heating of surrounding materials. Applying only the energy needed to process your parts is ideal.
Induction selectively focuses energy only on the area of the part that you want to heat. Each part in a process enjoys the same efficient application of energy. Since the energy is transferred directly from the coil to a part, there is no intervening media like flame or air to skew the process.
The precision and repeatability of induction heating help to reduce process scrap rate and to improve throughput. The selective application of heat to the targeted area of a part enables very tight control of the heating process, also cutting the heating time and limiting energy requirements.
Is Induction Heating More Production Efficient?
Delivering the highest quality parts for the least expense in the least time is accomplished with an efficient process, in which the input elements of materials and energy are tightly and precisely controlled. Induction heating’s targeted application of heat to the part or an area of the part, as well as repeatability, provides the most uniform results for the least cost. Repeatability and throughput are two things that can be greatly improved with induction compared to resistance or flame heating.
Induction heating delivers savings primarily from significant reductions in process scrap rates, improved throughput and from the thrifty use of energy. There is no need for process ramp-up; heat is applied and stopped instantly. In comparison, batch heating in an oven requires an investment of time and energy that serves only the process, not the product. Throughput and efficiency are increased by induction heating with the careful application of energy (heat) in amounts no more than required by the product.
Is Induction Heating considered to be a safe process?
Any heating process carries a risk of operator contact with the heated materials. A technology like induction heating that limits the extent of operator-contacted surfaces does reduce the overall risk. If heating can be limited to only the part and further limited to a zone of the part, safety is improved even more.
Compared to a flame or hand-held heating operation, each induction heat process cycle is identical, and the process requires no running adjustment. Therefore once established and proven, an induction heating process does not require highly-trained personnel to operate.
Let Us Help
We are dedicated to the whole customer experience. Our mission begins in THE LAB, where we solve our customers’ most challenging heating applications, identifying processes that can benefit from our remarkably reliable systems.
Our SmartCARE service personnel are trained to get and keep our customers up-and-running.
Solving Your Process Heating Problems
With a reputation for quality, built on over 30 years of experience, Ambrell provides innovative heating solutions. Our equipment is installed in over 50 countries and supported by a network of dedicated induction heating experts.
If you want to improve your heating application – anywhere in your process – consult with our team for high-efficiency and cost-effective solutions. Ambrell’s technical experts design and manufacture a range of induction heating systems to bring you the highest quality process heating solutions available.
Read our 8-page brochure; learn more about how the science of induction technology can solve your process heating problems.

About Induction Heating
Induction heating is a fast, efficient, precise and repeatable non-contact method for heating metals or other electrically-conductive materials. The material may be a metal such as brass, aluminum, copper or steel or it can be a semiconductor such as silicon carbide, carbon or graphite. To heat non-conductive materials such as plastics or glass, induction is used to heat an electrically-conductive susceptor, typically graphite, which then transfers the heat to the non-conducting material.
Read our 4-page brochure; learn more about how the science of induction technology can solve your precision heating problems.
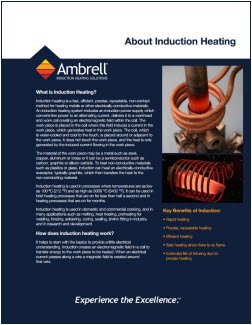
AMBRELL CORPORATION
1655 Lyell Avenue
Rochester, NY 14606
United States
Directions
T: +1 585 889 9000
F: +1 585 889 4030
Contact Sales
Contact Orders
Contact Service
AMBRELL B.V.
Holtersweg 1
7556 BS Hengelo
The Netherlands
Directions
T: +31 880 150 100
F: +31 546 788 154
Contact Sales
Contact Orders
Contact Service
AMBRELL Ltd.
Front Suite, 1st Floor, Charles House
148-149 Gt Charles Street
Birmingham, B3 3HT
United Kingdom
T: +44 1242 514042
F: +31 546 788 154
Contact Sales
Contact Orders
Contact Service