Note: Heating lead plates for a butt weld
Objective:
To heat two lead plates to temperature for a butt weld
End Product:
Lead plates
Equipment:
Ambrell EKOHEAT 50 kW, 15-45 kHz induction heating power supply with a remote workhead containing four 6.3 μF capacitors
A multi-turn helical induction heating coil designed and developed for this application
Materials:
Customer-supplied 0.5 in (13 mm) thick lead plates, 12 x 12 in (305 x 305 mm).
Temperature:
640 °F (338 °C)
Frequency:
39 kHz
Testing:
The end of the two plates were fluxed, placed on a ceramic plate and butted together. Ceramic blocks were placed at the ends of the joints. A steel weight was placed on top of the lead to hold it in place.
Induction power was turned on and the plates were melted at the joint/seam area within a 1 in (25 mm) melt zone and then the jointed areas were removed from the coil.
Testing proved the viability of the application, while the client will develop fixturing to hold the lead in place during heating and perfect the process.
Benefits:
-
Speed: The client was using a torch, which took five minutes; induction takes just one minute
-
Increased production rate: Faster heating means an improved production rate
-
Repeatability: Induction, unlike a torch, is precise and repeatable
-
Energy savings: Induction is a targeted, precise heating method which saves users energy
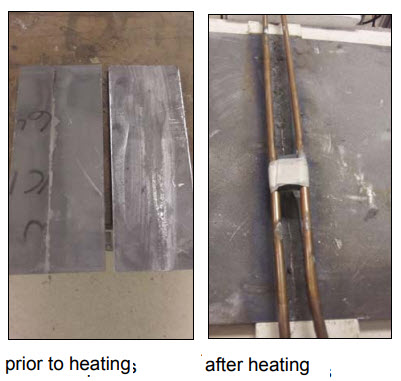
Visit our Applications Lab to learn more about free applications testing.
1655 Lyell Ave, Rochester, NY 14606 USA | Tel: +1 585 889 9000