Note: Preheating a titanium alloy wire prior to welding
Objective:
To preheat a titanium alloy wire prior to welding; the end product is an aerospace part
End Product:
Aerospace part
Equipment:
Ambrell EASYHEAT 10 kW, 150-400 kHz induction heating power supply with a remote workhead
A single position 38-turn helical coil with multiple water paths
Materials:
0.063 in (1.6 mm) diameter titanium alloy wire
Temperature:
2,732 °F (1,500 °C)
Frequency:
365 kHz
Testing:
Testing in static mode was done to simulate a dynamic feed rate of 8 in (203 mm) per second. While a static test may vary from dynamic conditions, it is a close simulation and used when test equipment is required to replicate a feed rate and is not available.
With an 8 in (203 mm) long coil and a feed rate of 8 in (203 mm) per second, any section of wire would spend one second inside the coil. Therefore, a static test of one second would simulate the performance of an EKOHEAT 10 kW power supply for the aforementioned feed rate. For each second added to the static test, it would simulate an additional 10 kW power supply heating the wire in series with other power supplies. With an EKOHEAT 10 kW power supply, the titanium alloy wire can be heated to 2732 °F (1500 °C) in three seconds. This testing configuration simulates using three EASYHEAT 10 kW power supplies in series.
Benefits:
-
Speed: Induction is a fast and repeatable solution for wire heating
-
Efficiency: Induction puts power right into the wire, so energy efficiency is maximized
-
Footprint: Induction requires a minimal footprint, saving valuable floor space
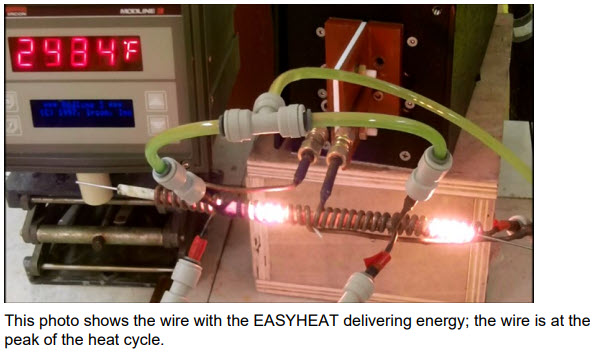
Visit our Applications Lab to learn more about free applications testing.
1655 Lyell Ave, Rochester, NY 14606 USA | Tel: +1 585 889 9000