Note: Preheating steel rods for a welding application
Objective:
To preheat steel rods to 500 °F (260 °C) for a welding application for a major equipment manufacturer
End Product:
Steel rods
Equipment:
Ambrell EKOHEAT 30/100, 30kW 50-150 kHz induction heating system equipped with a remote heat station containing eight 1.0 μF capacitors A multiple position two-turn induction heating coil designed and developed specifically for this application
Materials:
Customer supplied steel pins varying, on average 2 in (51 mm)
Temperature:
500 °F (260 °C)
Frequency:
100 kHz
Testing:
The steel rod was loaded into the coil, and the heat was turned on. The part reached 600 °F (316 °C) within one minute. The power was turned off and the rod was monitored for 30 seconds to ensure the outside layer did not drop below 500 °F (260 °C).
Based on the Application Lab's experiences and testing, the longer the heating time, the less power is required. Additionally, the longer the heating time, the longer the outside temperature remained above 500 °F. In light of that, there are additional possibilities when it comes to power supplies, from a 15kW EKOHEAT with a two-position coil that has a heating time of two minutes, to a 45kW EKOHEAT with a four-position coil and a heating time of one minute.
Benefits:
-
Precise heating: The customer is looking at switching from flame, as induction can offer more precise, repeatable heating
-
Penetration: Induction does a superior job penetrating the pin when compared to a torch, which is critical to preheating for welding
-
Speed: Induction enables fast heating which can boost production compared to torch heating
-
Part quality: A torch can make the part brittle, which makes induction advantageous Work environment: Induction is a safer heating method that introduces less heat into the workplace than a flame does
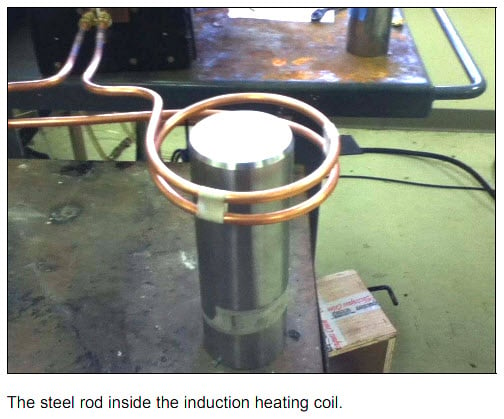
Visit our Applications Lab to learn more about free applications testing.
1655 Lyell Ave, Rochester, NY 14606 USA | Tel: +1 585 889 9000