Note: Wire stripping (heating varnish)
Objective:
Removal of electrical varnish from copper strands of various diameters
End Product:
Copper wire
Equipment:
Ambrell 10 kW solid-state induction power supply equipped with a specially designed heat gun with integral workhead and a work coil designed and developed specifically for this application.
Materials:
Copper cables with bundles containing from 1 to 32 strands wires/conductors from 0.6mm to 32mm diameter. Wires may be round, square or rectangular.
Temperature:
600 - 900 °C
Frequency:
50 - 150 kHz
Testing:
The individual conductors are simultaneously rapidly heated to destroy the bond with the varnish. The coil design ensures that all conductors in a bunch are evenly heated with handheld heat gun with an extraction port for connection to the extraction system. At the end of the heating cycle the cable remains in the gun until no more fumes come off. The cooling air stream is created by the extraction system. A lamp in the heat gun indicates the heat and post heat cooling portions of the cycle. When the lamp goes off the heat gun may be removed from the cable and positioned over the next cable. It is common to process a complete stator's worth of cables
(typically 12 or 24) prior to starting the next action, wire brushing. This allows as much time as possible for the conductors to cool so that the re-oxidization of the copper surface post brushing is minimized. The specifically designed pneumatically-driven wire brushing system is positioned over the cable and the trigger operated to start the contra rotating wire brushes. These are mounted on a pivot system controlled by the operator handle to regulate the brushing force. The wire brush system is moved on and off wire conductors in a reciprocating motion to ensure that all the debris is removed from the previously heated zone.
Both the heat gun and wire brush system are supplied with wire balancers to allow suspension from an overhead gantry rail (customer supplied). A PLC system controls the operation of the equipment and includes both heat and post-heat timers. The fume extraction system is controlled with an automatic shutdown after a few minutes of non use of either the heat gun or wire brush to protect the life of the filters. The multistage extraction system includes sensing equipment to control the vacuum level and cooling air flow within the work coil. This system has been supplied both as a single gun system and two gun system with an electrically operated changeover switch.
Benefits:
-
Increased production speeds. An electrical motor manufacturer slashed 500 man-hours per week production time (1 hour per motor). Typical manual stripping system with proprietary rotary strippers takes 75-90 minutes per motor (24 cables of 32 conductors). The induction system reduces this to below 15 minutes.
-
Cross-wire diameter remains the same.
-
Strands are annealed rather than work-hardened and ready for any method of termination. (This results in fewer gaps in the crimped zone. Crimping tools will require resetting to accommodate the improved crimping of the cable.)
-
Reduced joint temperature due in part to the lack of copper section reduction and the improved cross section after crimping (no air gaps)
-
Cleaner operator work station.
-
Improved system ergonomics with reduction in potential repetitive strain injury claims.
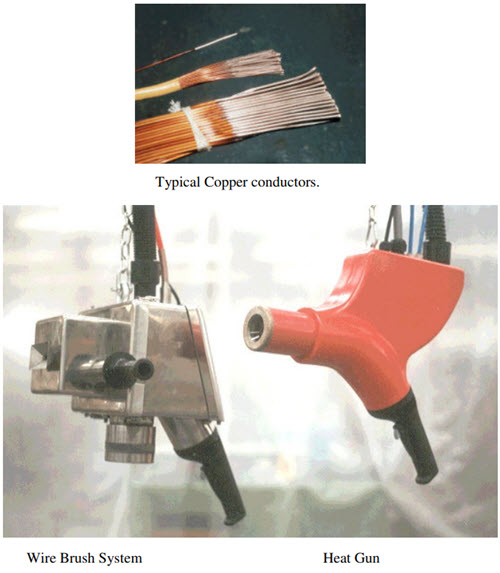
Visit our Applications Lab to learn more about free applications testing.
1655 Lyell Ave, Rochester, NY 14606 USA | Tel: +1 585 889 9000