Guide to Induction Coil Design
This brochure provides a guide for everything you need to design the optimal coil for the best performance from your induction heating system.
Induction heating coil design has a major impact on your part quality, process efficiency, and manufacturing costs. Click to get our 28-page brochure to help you design the optimal coil for your part and process. We provide excerpts below.
5 Basics of Induction Heating Coil Design
Induction coil design can have a major impact on part quality, process efficiency, and manufacturing costs. How do you know if your coil design is best for your part and process? Here are some induction coil basics and five tips to optimize your design.
How Induction Heating Coils Work
The induction coil determines how effectively and efficiently a workpiece is heated. Induction coils are water-cooled conductors made of copper tubing that is readily formed into the shape of the coil for the induction heating process. Induction heating coils do not themselves get hot as water flows through them.
Work coils range in complexity from a simple helical- or solenoid-wound coil (consisting of a number of turns of copper tube wound around a mandrel) to a coil that is precision machined from solid copper and brazed.
Coils transfer energy from the power supply to the workpiece by generating an alternating electromagnetic field due to the alternating current flowing in them. The coil’s alternating electromagnetic field (EMF) generates an induced current (eddy current) in the workpiece, which generates heat due to I Squared R losses (core losses).
The current in the workpiece is proportional to the coil’s EMF strength. This transfer of energy is known as the transformer effect or eddy current effect.
More about the 5 basics of induction coil design...
Designs & Frequency Selections
Induction coil design has a major impact on process efficiency and final part quality, and the best coil design for your product largely depends on your application. Certain coil designs tend to work best with specific applications, and a less than optimal coil-application pairing can result in slow or irregular heating, higher defect rates, and lower quality products.
Designing an induction coil for your application
Start with understanding where the heat needs to be generated in the part to perform the process, and then design the coil to achieve the heating effect. Similarly, frequency selection will depend on the induction heating application you’ll be using for your part.
Before designing your induction coil, consider these three factors along with your induction application:
-
Part motion relative to coil - Several applications rely on part movement with the help of conveyors, turntables, or robots. A properly designed induction coil incorporates these individual handling requirements without the loss of heating efficiency.
-
Frequency- Higher frequencies are used for applications like brazing, soldering, annealing or heat treating, where surface heating is desired. Lower frequencies are preferred for applications requiring through-heating of the parts to the core like forging and die heating.
-
Power-density requirements- Higher power densities are required for short cycle heating applications requiring high temperatures. Higher power densities may also be required to keep the hot zone confined to a small area, reducing the heat affected area.
Calculate Coupling Distance
Coupling is the transfer of energy that occurs in the space between the heating portion of the coil and the workpiece. So, coupling distance is how big that space needs to be to balance efficiency and manufacturing requirements.
Generally, distance increases with the diameter of the part, typical values being 0.75, 1.25, and 1.75 inches (19, 32 and 44 mm) or billet-stock diameters of approximately 1.5, 4 and 6 inches (38, 102, and 152 mm), respectively.
More about coupling distance...
Improve Heating Uniformity via Coil Design
Magnetic flux tends to concentrate toward the center of the length of a solenoid work coil. This means the heating rate produced in this area is generally greater than that produced toward the ends. Further, if the part being heated is long, conduction and radiation remove heat from
the ends at a greater rate. The coil can be modified to provide better heating uniformity along the part length. The technique of adjusting the coil turns, spacing, or coupling with the workpiece to achieve a uniform heating pattern is sometimes known as “characterizing” the coil.
- Coil characterization
- Six other common ways to improve heating uniformity
- Heating two separate areas on a part
- Heating tapered parts
- Heating a part with secondary fabrications
- Heating a variety of different parts with one coil
6 ways to improve uniformity of heating...
Solenoid Coil Designs & Calculations
The type and design of the induction coil determines how effectively and efficiently a workpiece is heated. Work coils range in complexity from a simple helical- or solenoid-wound coil (consisting of a number of turns of copper tube wound around a mandrel) to a coil that is precision-machined from solid copper and brazed.
The helical solenoid coil is the most ubiquitous induction coil design. It provides a wide range of heating behaviors since the part or heating area is located within the coil, in the area of greatest magnetic flux. Flux lines in a solenoid coil are concentrated inside the coil, providing the maximum heating rate at that location.
More about efficient solenoid coil design...
Need an Induction Coil Built?
Ambrell has a wealth of experience building induction coils. Whether you need a coil built for an Ambrell induction heating system or another induction system, we can help. Reach out to us to get the process started.
About Induction Heating
Induction heating is a fast, efficient, precise and repeatable non-contact method for heating metals or other electrically-conductive materials. The material may be a metal such as brass, aluminum, copper or steel or it can be a semiconductor such as silicon carbide, carbon or graphite. To heat non-conductive materials such as plastics or glass, induction is used to heat an electrically-conductive susceptor, typically graphite, which then transfers the heat to the non-conducting material.
Read our 4-page brochure; learn more about how the science of induction technology can solve your precision heating problems.
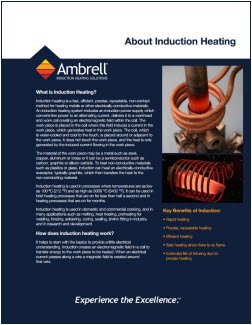
Induction Heating Work Coils
The work coil is the component in the induction heating system that defines how effective and how efficiently your work piece is heated.
Read our informative brochure explaining the fundamentals of induction coils and their design.
Read Read: Induction Heating Work Coils

AMBRELL CORPORATION
1655 Lyell Avenue
Rochester, NY 14606
United States
Directions
T: +1 585 889 9000
F: +1 585 889 4030
Contact Sales
Contact Orders
Contact Service
AMBRELL B.V.
Holtersweg 1
7556 BS Hengelo
The Netherlands
Directions
T: +31 880 150 100
F: +31 546 788 154
Contact Sales
Contact Orders
Contact Service
AMBRELL Ltd.
Front Suite, 1st Floor, Charles House
148-149 Gt Charles Street
Birmingham, B3 3HT
United Kingdom
T: +44 1242 514042
F: +31 546 788 154
Contact Sales
Contact Orders
Contact Service